Cost Estimation Trends Q2 2025
Labor Shortages, Apprenticeships, and the New Reality Impacting Construction Costs
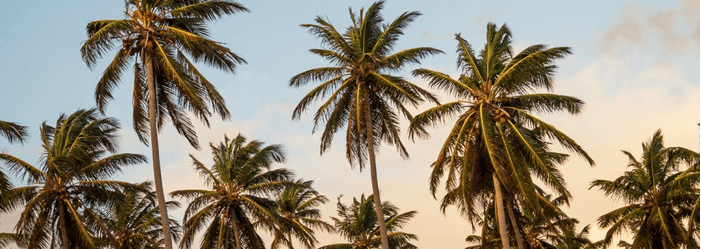
If you are planning a construction project in 2025 and beyond, you need to factor in two unstoppable forces: volatile costs and chronic labor shortages.
These are major factors in today’s marketplace and can impact costs substantially. We are talking about structural changes that are reshaping how projects are priced, staffed, and delivered, right now.
1. Escalation Is Still Alive and Well
Despite hopes that inflation would cool, major construction materials continue to rise:
●
Concrete: Costs have surged 6.7% year-over-year
●
Structural Steel: Up 5–7% even after last year’s big jumps
●
MEP Equipment: Lead times are stretching to 6–12 months with prices 10–15% higher
If your team is still relying on unit costs from 2024, you are navigating blindfolded.
Costs change weekly. Estimating based on outdated data is no longer just risky. It is reckless.
2. Labor Shortages Are Getting Worse, Not Better
The US construction industry needs
439,000 new workers in 2025 to meet current demand.
Wages have risen
4.5% over the past 12 months, and productivity is sliding as firms scramble to train replacements on the fly. Apprenticeships are down. However, with the Executive Order announced on April 23, there is a fresh Federal push to expand registered apprenticeships across high-demand industries, including construction.
The goal?
●
1 million new active apprentices nationwide
●
Focused investment in workforce development
●
Potential support for both union and non-union training pathways
It is a smart move, but even if fully successful, these programs will take years to materially impact the workforce shortage we are seeing today. It takes time to source and train productive workers, especially in complex trades such as mechanical and electrical. Costs will still have to reflect low labor productivity and lack of skilled workers.
Labor gaps or shortages will require premiums to be added to reflect low productivity, added supervision, training costs, added health and safety requirements and prolonged schedules with associated cost to critical activities. We are also seeing scheduling impact charges, rush premiums, padded contingencies all driven by labor gaps.
3. What This Means for Project Costs and Planning
The ripple effects are immediate and real:
●
Less competition: Mid-size public projects that once attracted 8–10 bidders are now lucky to get 2–3. Less competition means higher bids.
●
Risk pricing is baked in: Contractors are submitting more conservative bids because they know volatility and higher labor costs are here to stay.
● Estimates are routinely 10–12% higher than planned, even when forecasting is conservative. Proformas and project budgets can be blown early in the design cycle if estimates are not realsitic.
4. What Smart Owners and Developers Are Doing
In this climate, the most successful teams are shifting how they think about cost management:
●
Initiating value engineering (VE) early instead of waiting until bids come in
● Negotiating escalation clauses into contracts, especially for long-lead items
● Be open to material and equipment alternatives to assist with competition in terms of costs and schedules
● Proactively market your project to gain awareness of the project and obtain more bids reducing costs through market forces
●
Demanding real-time cost intelligence from estimators, not relying on static quarterly reports
● Integrating estimators into the design process rather than sporadically getting estimating involvement. Make the estimator provide continuous input on materials and system selections early in the design process.
Proactivity beats passivity.
Real-world data beats assumptions.
Partnership beats blame games.
Final Takeaway
The construction world of 2025 is different. Labor markets are fractured. Materials are volatile. Costs will continue to shift under your feet.
Apprenticeship expansion and federal workforce initiatives are steps in the right direction.
If you are building today, you cannot wait for Washington to solve your project problems.
You need real intelligence, real flexibility, and real strategy, now.
If you would like to receive additional insights or discuss a project, feel free to send us a DM. Primestone is here to assist with estimating, project advisory or expert witness services.
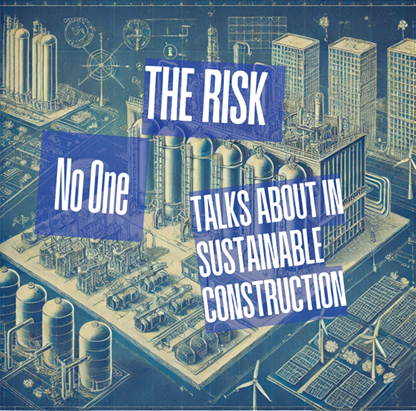